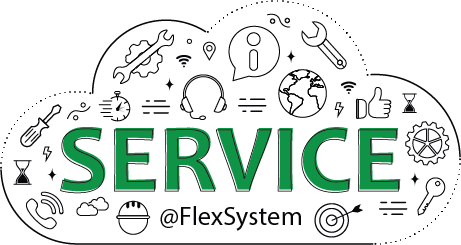
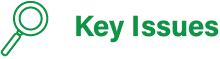
With a hundred or more daily repairing cases, traditional manual document and business processing is no longer able to fulfill the continuous expansion for extensive services and internal information tracking and monitoring.
- Communication issues between customer service and internal engineers.
- Limited data security and increased risk of data loss.
- Difficulty in standardizing the approval process.
- Inability to monitor process status online.
- Reporting challenges without system automation.
- Difficulty in evaluating staff productivity.
- Risk of damage or loss of paper documents.
- High operation and administration costs.
- Transaction processing delays between engineers.